1. Precise Control of Formula
Precise Weighing of Raw Materials: Use automatic metering systems (such as loss-in-weight feeders) to ensure consistent ratios of different raw materials.
Uniform Mixing: Use high-efficiency sigma mixer and reactor to ensure that resins, tackifiers, antioxidants and other ingredients are fully mixed.
2. Stability and Precise Control of Equipment
Reactor (applicable to polymer hot melt glue)
- Temperature Control System: Use jacket heating or coil heating, combined with PLC automatic control to ensure constant temperature and avoid viscosity and fluidity affected by overheating or overcooling.
- Stirring System: Accurately design the stirring speed and blade structure to heat the material evenly and avoid local overheating or uneven mixing.
Sigma Mixer (applicable to rubber-based hot melt glue)
- Ensure stable kneading time and shear force to avoid differences in molecular structure between batches.
Extrusion Granulator (applicable to EVA, PO hot melt glue)
- Constant screw speed to prevent uneven shearing of materials from causing product specification deviations.
- Pressure, temperature and shear rate are kept consistent to prevent insufficient melting or degradation.
Filtration and Degassing System
- Use high-precision filters to remove impurities and avoid uneven particles in the finished product.
- Use vacuum degassing to prevent bubbles from affecting the uniformity of the colloid.
3. Standardized Operation and Maintenance
- Establish standardized SOP (standard operating procedure) to ensure that workers strictly follow the parameters.
- Maintain the equipment regularly to ensure that the stirring blades, temperature control system, filtration system, etc. are in the best condition.
- Calibrate sensors and testing equipment regularly to prevent quality fluctuations due to sensor errors.
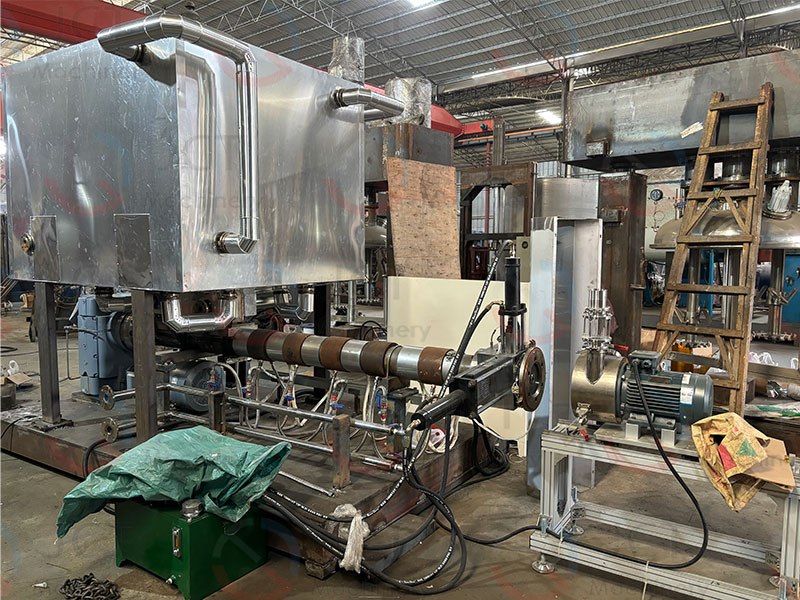
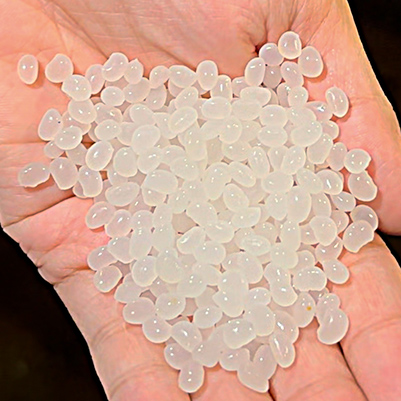
Hot melt glue granules made by JCT production line equipments are uniform in size and have no residual wire drawing.